The Cartographer of Silence: Mapping the Internal Landscapes of Record Players
There's a quiet dignity to antique phonographs. Not the boisterous confidence of modern technology, but a gentle, enduring presence. They’re relics of a time when entertainment was an event, a communal experience woven into the fabric of home life. Repairing one isn’t just about fixing a machine; it’s about connecting with a forgotten era, understanding the meticulous craftsmanship of the engineers who conceived them, and, in a strange way, listening to the echoes of countless stories they've preserved.
I remember the first phonograph I encountered. It was my grandfather’s, a Majestic Victrola, shrouded in dust and silence for decades. As a boy, I'm not sure I understood *why* it was special, beyond the fact that it was old and interesting. But the act of my grandfather, carefully dusting it off and winding the spring, felt imbued with a ritualistic reverence. The moment the first crackling note filled the room – a scratchy rendition of a forgotten ragtime tune – felt monumental. It wasn't just music; it was a portal.
The Terrain Unveiled: Anatomy of a Phonograph
To truly understand a phonograph, to truly repair it, you need to see it not as a collection of parts, but as a carefully designed ecosystem. Let’s begin our cartographic expedition, charting the key features of a typical mechanical phonograph. At its heart lies the driving mechanism – often a spring-powered motor, meticulously wound and releasing its energy to turn the platter. This platter, the stage for the vinyl performance, must be perfectly flat and balanced. A warped platter throws the entire system out of alignment, leading to skipping and uneven sound. Above the platter sits the tone arm, a delicately balanced lever holding the stylus – the needle that traces the grooves of the record.
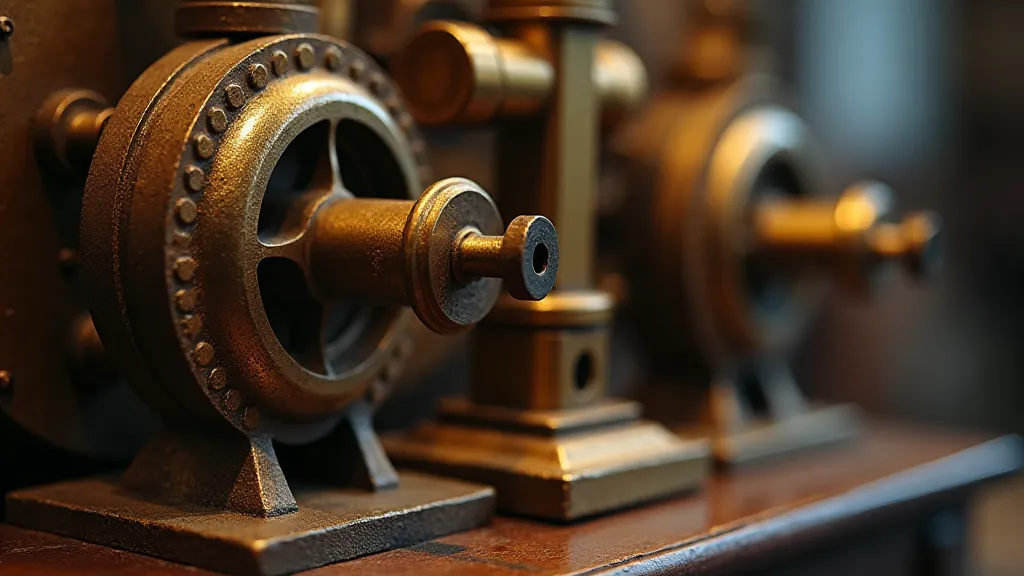
The stylus itself isn’t just a needle; it’s a tiny transducer, vibrating in response to the microscopic undulations in the record grooves. This vibration is then transmitted to the sound box, a marvel of acoustic engineering. In early models, the sound box relies on a diaphragm – a thin, often beautifully decorated, membrane that vibrates and amplifies the sound. These diaphragms, often made of paper, cloth, or even metal, are notoriously brittle with age and easily damaged. Ensuring the smooth operation of these complex mechanisms, especially the motor itself, is a constant challenge – and sometimes requires a full replacement of the drive belt to restore proper function.
Common Ailments and Their Cartographic Challenges
The passage of time takes its toll. Like any explorer encountering a treacherous landscape, a phonograph repairer must be prepared for a variety of challenges. One of the most common is a seized motor. Dried grease and decades of inactivity can bind the gears, rendering them immovable. Careful cleaning and lubrication, using appropriate oils designed for vintage machinery, is often the solution. However, sometimes more extensive repairs are needed, involving the dismantling and cleaning of individual gears. The underlying reason for the seizing might also point to larger issues with the drive mechanism.
Warped platters present another cartographic conundrum. While some warping can be mitigated through careful storage and handling, severe warping often necessitates a difficult choice: attempt a delicate flattening process (often involving heat and pressure, a risky endeavor) or seek out a replacement platter. The scarcity and cost of replacement parts can often dictate this decision. The impact of these machines extended far beyond individual homes; understanding the social impact of antique phonographs provides valuable context when attempting restoration.
Brittle diaphragms are perhaps the most heartbreaking ailment. A tiny tear, a hairline crack – these seemingly minor flaws can severely impact the phonograph’s sound quality. While skilled restorers sometimes attempt to repair these tears, often the only viable option is to find a replacement. The hunt for authentic diaphragms can be a quest in itself, involving scouring antique shops, online auctions, and connecting with specialized phonograph parts dealers.
The Whisper of History: More Than Just Mechanics
Repairing antique phonographs isn't solely about the mechanics. It’s about understanding the context in which they were created. Consider the materials used – the quality of the metal, the precision of the machining, the artistry of the decorative elements. These weren’t mass-produced items churned out by automated assembly lines. They were crafted by skilled artisans who took pride in their work. Each phonograph tells a story – of the factory where it was built, the family who owned it, the music that filled the room.
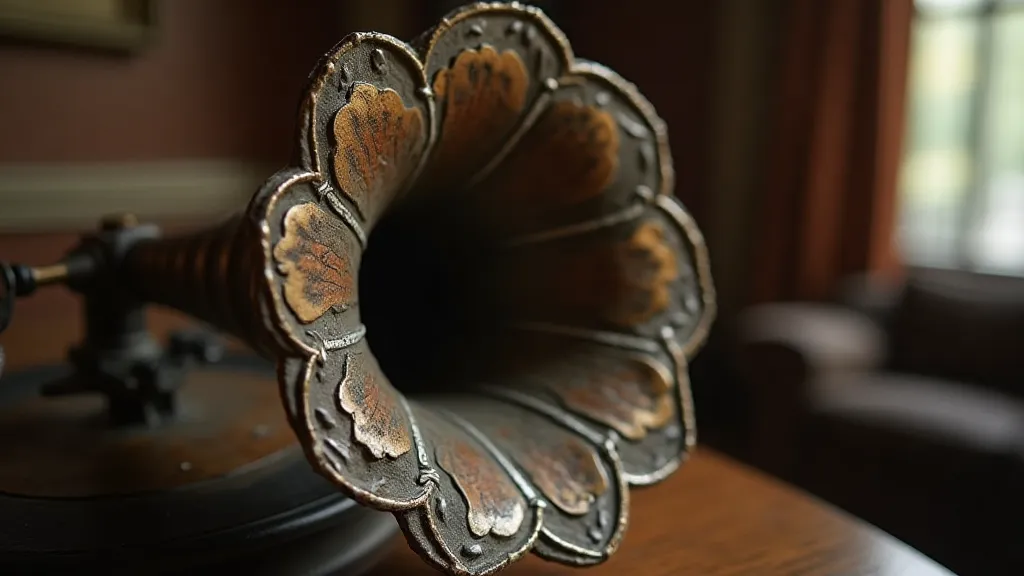
The process of restoration can be a profoundly rewarding experience. Holding a piece of history in your hands, carefully cleaning away the grime of years, and slowly bringing it back to life – it’s a connection to the past that few experiences can match. It's not just about fixing a machine; it’s about preserving a legacy, a tangible link to a simpler time. You begin to appreciate not just the sounds the phonograph *can* produce, but also the stories it holds within its silent form. Preserving not only the internal workings, but also the beautiful exterior cabinetwork is a critical part of the restoration process, and the art of cabinet restoration demands a different skill set entirely.
Beyond the Repair: Collecting and Appreciation
For some, the pursuit of phonograph repair blossoms into a passion for collecting. The world of antique record players is vast and varied, ranging from the iconic Victrola to the more obscure cabinet models. Building a collection requires more than just a keen eye for aesthetics; it requires an understanding of different manufacturers, models, and their historical significance. Issues like spring tension and wear are also key to assessing a phonograph’s value and collectibility, and common spring problems frequently arise during inspection.
But even if collecting isn't your goal, simply appreciating the beauty and ingenuity of these machines is a worthwhile endeavor. Take the time to examine one closely. Notice the intricate details, the clever mechanisms, the enduring elegance. Listen to the music it produces – not just for the notes themselves, but for the echoes of the past they carry. The sheer variety of models and designs underscores the ingenuity of the era, and understanding the materials and techniques employed adds another layer of appreciation.
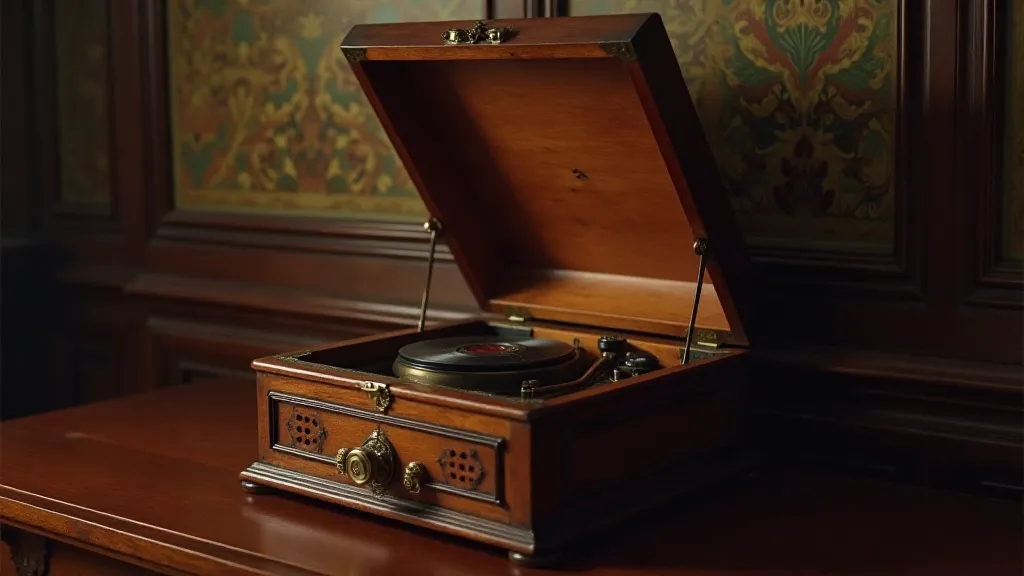
Repairing antique phonographs is, at its core, an act of reverence – a cartographic exploration of a landscape of silence, a testament to the enduring power of music, and a tangible connection to the ingenuity of the past. Each restored phonograph isn't just a machine that plays music; it's a portal, a storyteller, a living testament to a time when the simple act of listening was a shared and cherished experience. The challenges involved in bringing these machines back to life are numerous, requiring a blend of mechanical skill, patience, and a deep respect for history. Beyond the immediate task of repair, there's a broader appreciation for the craftsmanship and artistry of a bygone era, a time when objects were made to last and music was a shared experience, not just a solitary pastime. Understanding the complexities of these machines and the social context in which they thrived provides a richer understanding of both the technology and the culture of the early 20th century.
The dedication required to preserve these historical artifacts ensures that future generations can experience the magic of these early sound machines. The echoes of the past resonate within each restored phonograph, a testament to the enduring power of music and the ingenuity of the human spirit.